Technology
Technology
Four Advantages
-
Advantage.1IATF16949, the latest international standard
IATF16949 is an international automotive QMS standard. Many automobile manufacturers in the world are adopting it as a global procurement standard, and we continue to maintain the latest version of internationally recognized QMS at all times.
-
Advantage.2No.1 in the world
Our products, tappets are adopted as a luxury car of the world’s leading automobile manufacturer. We are aiming for the No.1 in the world with advanced technology that others cannot catch up.
-
Advantage.3Approved as a “Preferred Supplier”
Tappets for clean diesel engines require high turning and grinding precision, our products are used not only in automobiles, but also in agricultural machinery such as tractors, ships, and electric generators, which are active in a wide range of fields.
-
Advantage.4The areas for using the techniques expand
Tappets for clean diesel engines require high turning and grinding precision, our products are used not only in automobiles, but also in agricultural machinery such as tractors, ships, and electric generators, which are active in a wide range of fields.
Our technology supporting precision processing
Grinding / Polishing / Superfinishing
- Flat and cylindrical surfaces, inside/outside diameters, seating surfaces
- Spherical end faces, basin surfaces
- Crowning, multiple crowning
Precision processing at sub-micron level
Turning
- High-precision turning technology realizing more efficient and precise grinding at later stage
<Examples of our precision parts>
Precision measurements
- Surface roughness and form measuring device
- Roundness measuring device
- Precision microscope
- 3D measuring device
- Hardness measuring device
- Image dimension measuring machine … etc.
Supply chain management
- Forging: Cold forging of bearing steel (JIS SUJ2)
- Heat treatment
- Surface treatment
- Precision turning
- Material developments
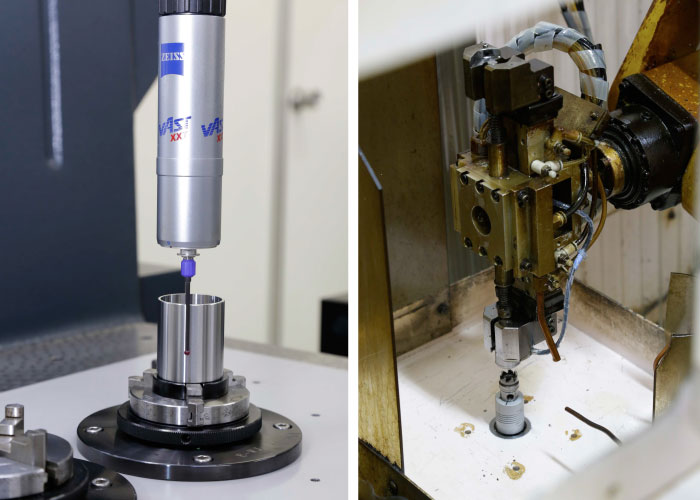

High-precision processing technology (Examples)
What is superfinishing?
Superfinishing is a method to obtain a smooth and highly precise surface that is achieved by pressing fine grindingstones against the part surface with low pressure and then making micro-motion turning through oscillation.
This superfinishing method realizes low heat generation through low pressure/speed operation and removal of subsurface damage. Since the superfinishing processing provides improved wear resistance, corrosion resistance and lubricity of surface, it is suitable for wear parts with high abrasive wear.
Various types of superfinishing
Noguchi Seiki provides various types of superfinishing processing, not only for inside/outside diameter of cylindrical parts but also for other shapes. Some examples are presented below:
■ Crowning
Crowning is a method whereby the surface of cylindrical parts is ground to a slightly barrel- shape (i.e. convex).
By the crowning process, it can be realized to reduce the edge loading at the contact area between the rolling contact surface and the track surface, and to make the pressure distribution uniform.
Besides the simple convex form indicated above, we provide crowning processing with various different types of crowning form.
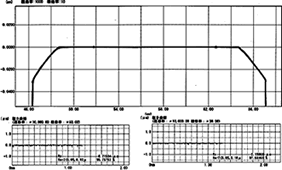
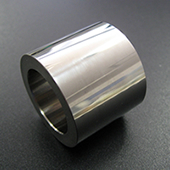
■ Superfinishing of basin surfaces
Superfinishing the flat sliding surfaces to a basin concave/convex shape helps equalize the pressure distribution at the contact area.
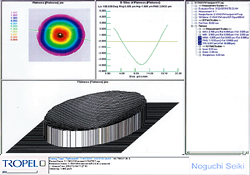
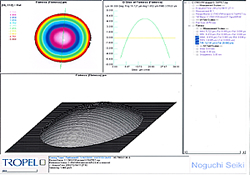
■ Superfinishing of spherical end faces
By superfinishing the end surfaces of high-speed rotation parts to a spherical form, the contact area is reduced and the friction is suppressed.
We use the only-one machine in Japan for this superfinishing processing.
Technical Catalog
Technical Catalog
Noguchi Seiki's technology is summarized in a catalog.
■ Catalog Download
-
Technical Catalog